Emily Bellinger, an adjunct faculty in the School of Art and School of American Craft, is a fine art quilter and bag maker. Soon after a friend asked her to make a personal fabric mask and an image of it was posted on Instagram, the orders flooded in by the hundreds. To date, she has produced several hundred masks in the last few weeks and has about many more on order. Because of the quantity and the immediacy, her partner, Visiting Lecturer in the School of Photographic Arts & Sciences Kes Efstathiou took the role of prepping all the masks, including ironing, cutting, managing orders, packing shipments, and driving orders around. Local restaurants are putting in bulk orders, and some are being shipped to as far away as California.
Interview by Laura Robak
Photos and Videos by Kes Efstathiou and Emily Bellinger
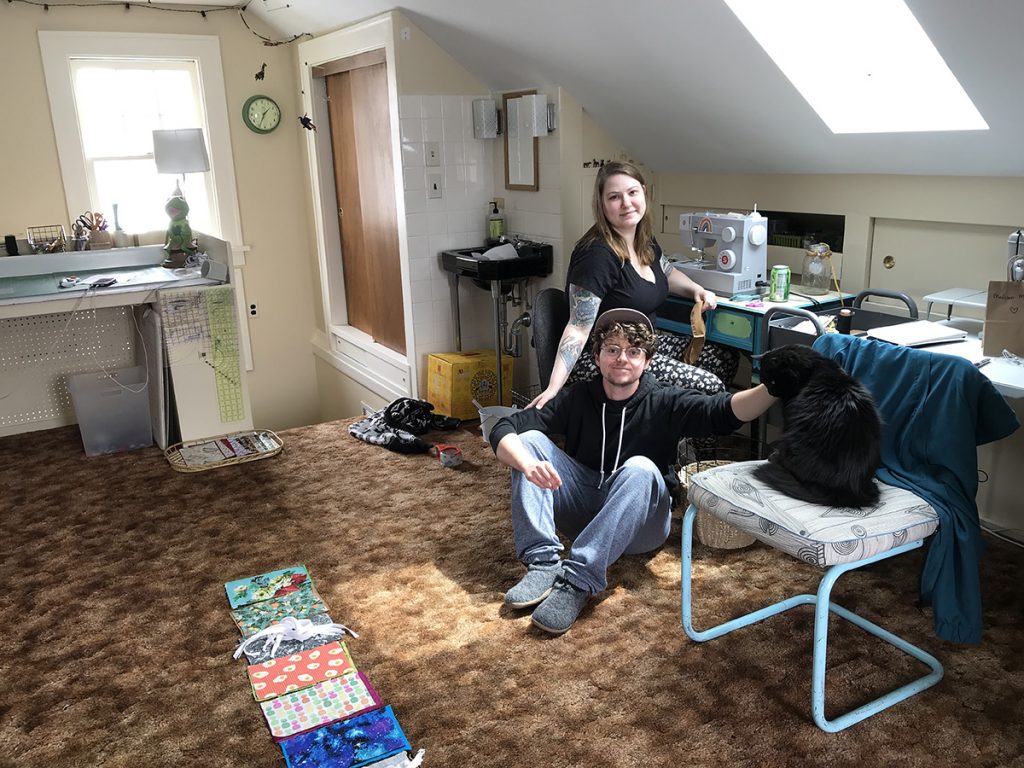
Did you ever think you’d be in this role as artists?
Emily: No but I am glad my skills can be used to provide a necessary product during this crazy time. I was hesitant at first with all of the controversy around handmade masks, but a friend in Chicago reached out and asked if I could make him some custom ones. I shared the post on Instagram and several people began contacting me asking me to make masks for themselves, friends and family. It boomed overnight. Once New York state required everyone to wear masks in public, I had hundreds of orders. I don’t have the exact number right now but I have probably made over 500 masks.
What’s been the most gratifying part or most rewarding?
Emily: Everyone is really thankful and it feels good to help out. Also, It’s been super fun to work with Kes on a project. He cuts a mean rectangle and keeps me calm when I start to stress about the number of orders. He also mixes up my music when I have listened to Slide by the Goo Goo Dolls too many times.
Kes: I am a very active person and I love a schedule. After about a week of this mess. I was all out of whack. It was nice to have a project to put my energy into. I didn’t have to question what my day would look like, it was simple, I would teach and then prep masks.
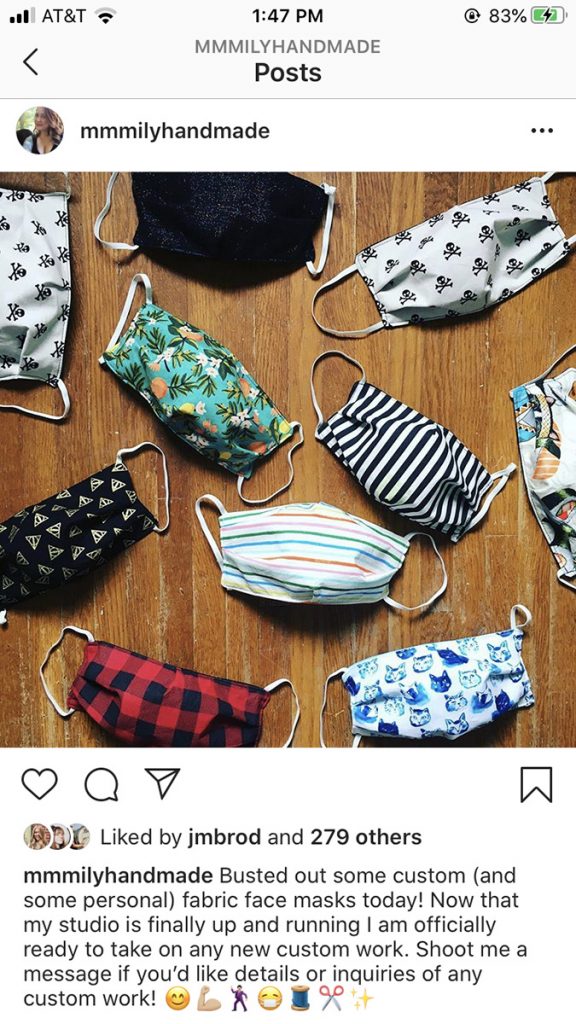
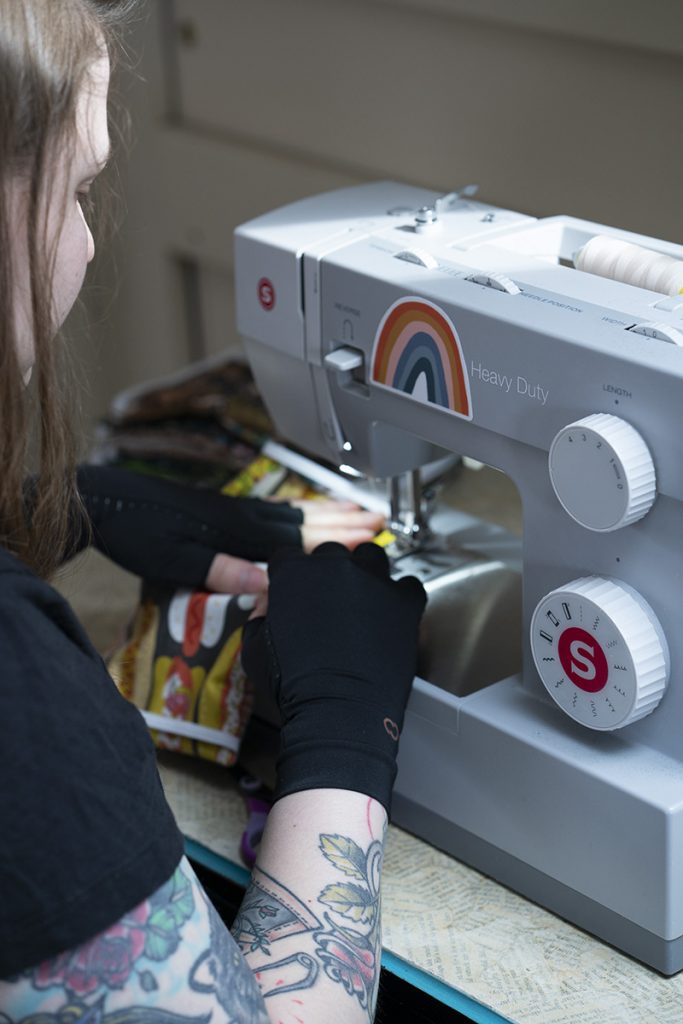
What’s been the hardest part or least rewarding?
Emily: Keeping up with the demand has been hard. Customers obviously want their masks ASAP, but I have to make each one it takes time. I also need time for self-care. The first few days we were working about 10-12 hours, we took a day off and tried really hard not to feel guilty about it.
Kes: All small businesses are doing what they can to stay afloat it’s cool to see people support Emily’s business. We are shipping masks all over the States, but it is nice to have so much of the local community support.
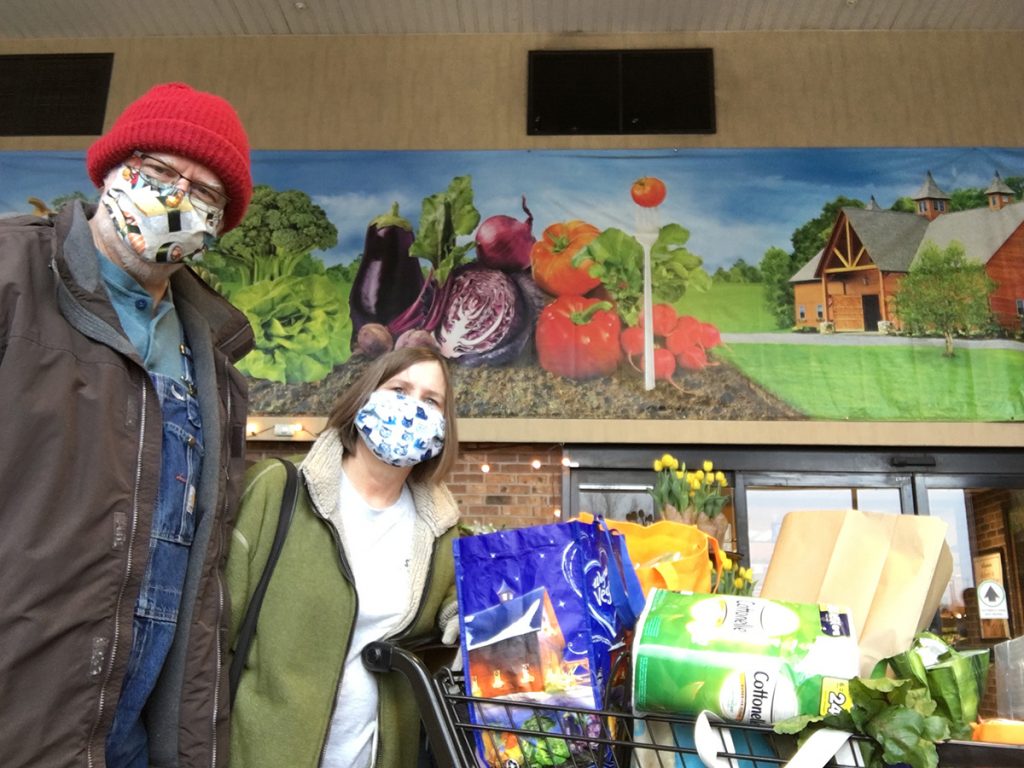
What are some of the things you’re hearing from folks who have benefited from the equipment you’ve made?
Emily: People are really nice. I love when people tag me in their Instagram selfies. I am having several repeat customers ordering even more masks. That is tangible feedback that proves people are satisfied and happy to support.
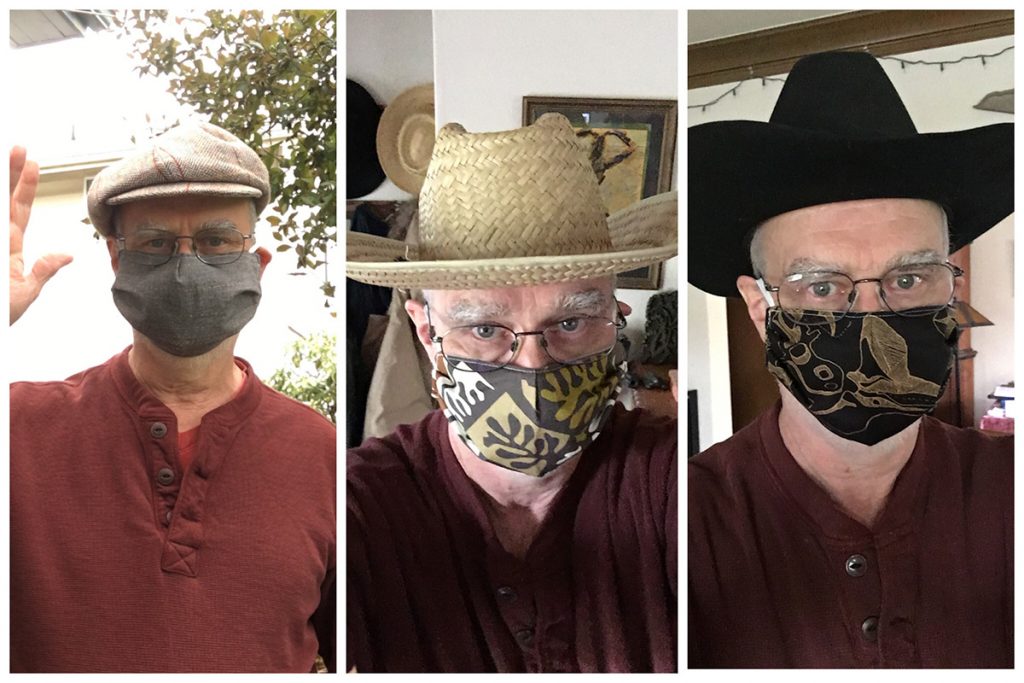
How have you changed the designs based on feedback from your users?
Emily: It’s been hard to make a one size fits all product without proper time to test it out. Of the hundreds of customers, two have complained about the fit (one too small and one too big). We suggest that if people are stressed about the fit, they should order ties instead of elastic.
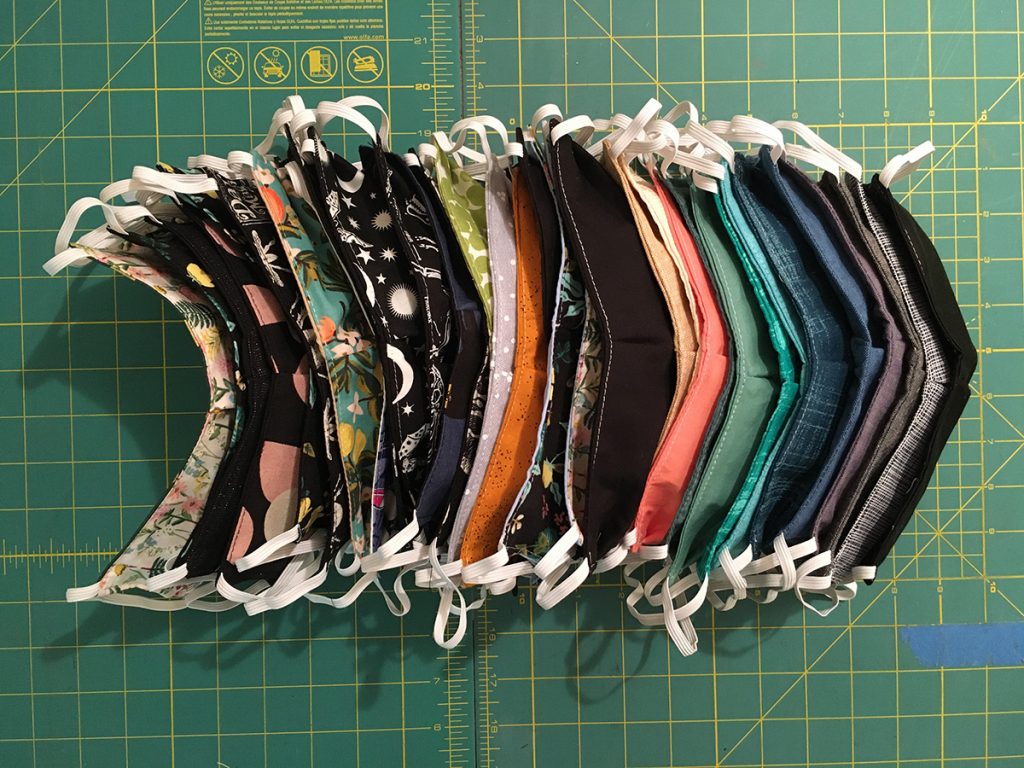
Did you have to read up on how to make them work the best, in other words, be most effective at preventing the spread vs. just looking and fitting well?
Emily: My design is well researched but they are for personal use and are not medically safe. They have 2 layers of cotton and a layer of fusible interfacing in the center. I also offer masks with filter pockets instead of interfacing if people want to go that route.
What reflections or take-aways do you have from this experience?
Kes: I hope that mask-wearing becomes an integrated part of our culture, like in many parts of Asia